Subsoil offers the construction industry a hybrid solution; not only does it help reduce our reliance on natural resources – like sand and aggregates – but it also holds natural properties that can contribute to building efficient and comfortable environments – thermal inertia, hygrometric regulation, heat storage capacity, to name a few. Think about it this way: we can build walls, and floors, that keep our spaces cool in the summer and warm in the winter, regulate humidity levels, and purify the air, all while achieving significant carbon reductions.
The architecture firm Bennetts Associates’ Tribeca project, a mixed-use development in the heart of London’s biotech district, is the first building of its scale in the United Kingdom to adopt subsoil as a construction material.
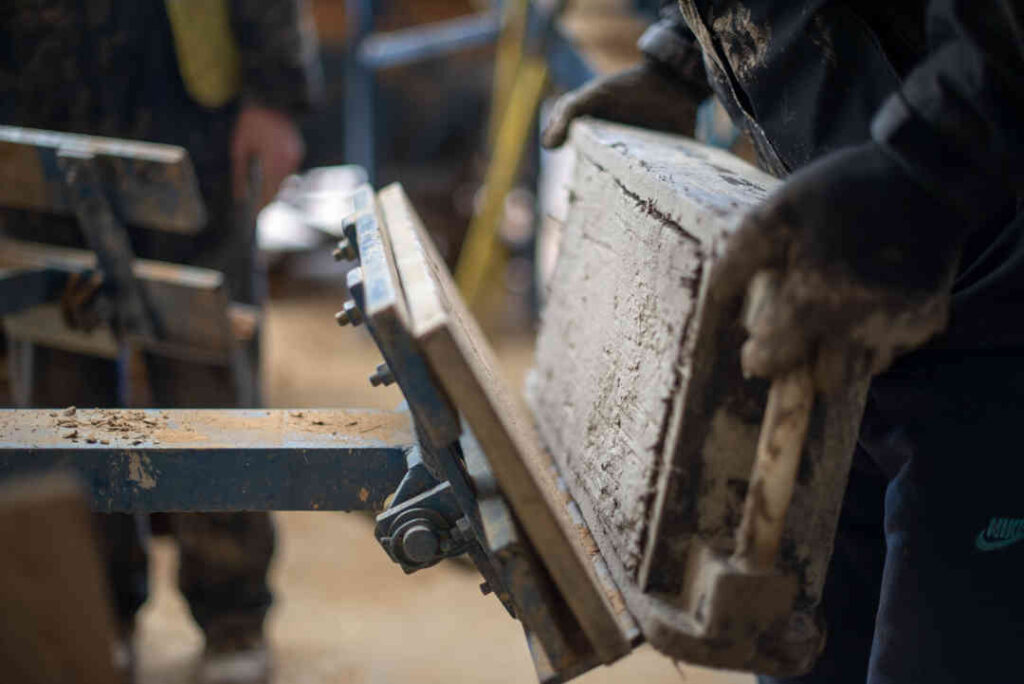
“Usually, we take the soil we excavate out of the city and we pay to get rid of it in landfill sites,” explains Nikolay Shahpazov, associate architect at Bennetts Associates. “Instead of having concrete blockwork, we came up with the idea to take this soil, bring it to a soil manufacturer, balance out the mix and send it back as blocks to be used,” he adds.
In all stages of development, the soil undergoes a series of tests to ensure its quality and performance. They first sample the soil on the site and test it as an earth block mix, making sure there is no contamination. Later, the blocks undergo a series of technical tests, including compression and fire-resistance, to secure its technical properties. In Tribeca’s case, the deep strata of the clay extracted was very stiff and yielded a performative and strong earth block, which was later taken into production.
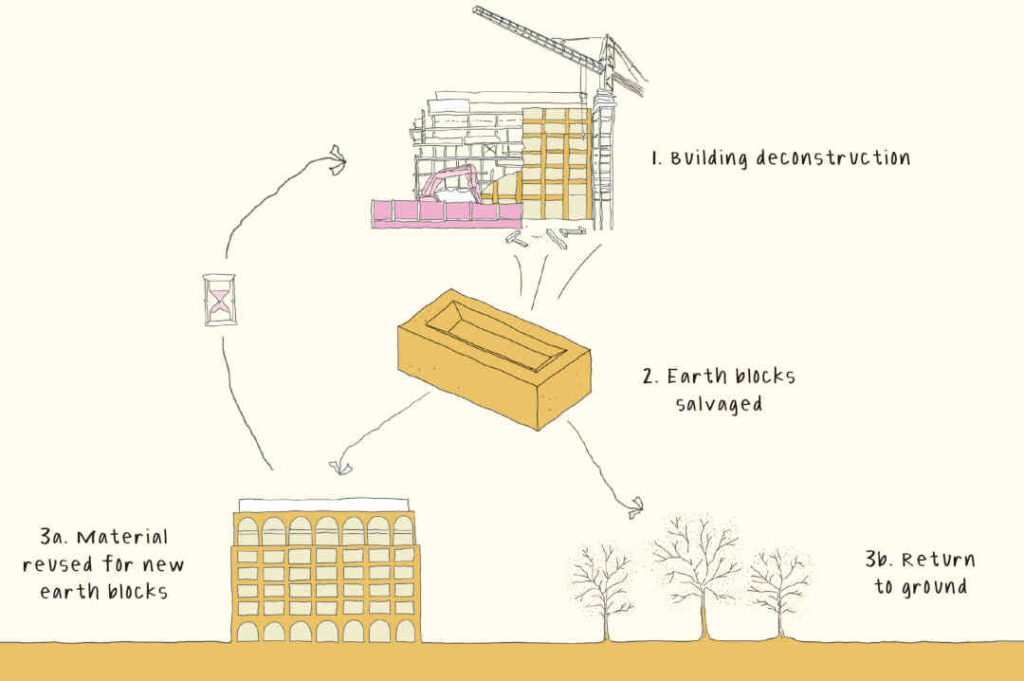
10 times less carbon emissions than concrete blocks
The embedded carbon associated with producing the blocks—extracting the soil, transporting it to a manufacturer, transforming it into a block, and taking it back to the construction site to be implemented into the building—is one-tenth of the embedded carbon of concrete blocks. “If you think about the scale of change, if each new building represents one-tenth of business as usual, you start to think you’re on the right track. We hope there will be many more and that it will trigger a big change in the industry,” Shahpazov states.
Excavated soil holds numerous qualities: it can be transformed into a durable product and used for new constructions and renovations, and, at the end of its lifecycle, broken down and reused, or sent back to nature. Cost-wise this alternative, which is often seen as extravagant or costly, is in the end comparable to traditional blockwork construction.
Initiatives around the world
More and more different organizations are starting to position this new material as a sustainable building choice in the region. In Belgium and France, companies like BC Materials, Amàco, and Cycle Terre are developing similar subsoil products for the market. The technique is more common practice in countries where architects and developers tend to take advantage of this ancient practice to build using local resources. In 2001, the Pritzker Prize-winning architect Diébédo Francis Kéré built his first school in eastern Burkina Faso out of clay, adding cement to make the bricks. In 2010, Studio Mumbai built Copper House II in India using excavated soil to make an artesian well (which brings groundwater to the surface without using a pump). These are just a few projects in a rather large roster of structures erected using local excavated soil in these regions.
Changing the practice of an entire industry will not happen overnight. Yet there are other stumbling blocks—impacting change in the construction sector is a slow process, and adapting to new ways of building is often difficult for developers and structural engineers. For years European stakeholders have been trained to build using concrete, steel, and glass.
“The industry isn’t prepared for this,” explains Shahpazov referring to the lack of awareness and knowledge about the material, “we tend to stick to what we know, but the situation is gradually improving.”
Photo credits: © stevecoleimages via iStock.com © Will Claxton / Urban R © Bennetts Associates