What is your role as Vinci’s Global Head of Environment?
Isabelle Spiegel: I joined Vinci in 2019, at a time when the Group decided to take environmental issues into consideration at an accelerated pace. For over a decade, a manifesto has provided a framework for our CSR commitments. We said to ourselves that we had to be even more proactive in this respect. My role was to define the environmental strategy linked to this acceleration for 2020-2030 and guide the operational staff in its implementation. This approach has three parts. The first — Acting for the climate — with greenhouse gas emission reduction targets at Group level: 40% fewer direct emissions by 2030, in other words, with regard to scopes 1 and 21, and 20% fewer indirect emissions, i.e., scope 31. The second — Optimizing resources thanks to the circular economy — to limit the footprint of the Group’s activities, with the specific goal for Vinci Construction of doubling our recycled aggregate production by 2030. Finally, the third — Preserving natural environments — which involves our real estate development activities with the goal of zero net land take in 2030.
Of course, while the strategy and targets are designed to remain stable over time, current events or regulations may lead us to accelerate certain forms of implementation. For example, since September 2022, we have been rolling out a long-term electricity and natural gas savings plan in France, thus helping limit the risks concerning the supply of these energies.
In which areas have you particularly innovated over the past few years?
I. S.: There are many, but if we had to choose two, I would like to talk about materials and renovation. We have been working on low-carbon concretes for five years now. As a reminder, the extremely carbon-heavy part of concrete is cement. We therefore encouraged R&D to see if we were capable of manufacturing cement-free concrete, in other words using cement substitutes, such as steel slags2, which are — for good measure — derived from the circular economy. This led to the first practical implementation over two years ago on the structural posts at l’archipel, our headquarters in Nanterre (France). Since then, this experiment has been repeated all across France and the world — New Zealand, England, Cambodia, etc. Line 18 of the Grand Paris Express, the City Rail Link in Auckland, London’s LGV High Speed 2 project, the drinking water treatment plant in Bakheng. We have thus completed around 25 projects of this kind, thanks to a material-based innovation as well as the implementation of a strategy and new ways of working with suppliers.
In the field of renovation, we have, for example, developed the Rehaskeen® solution, which makes it possible to significantly speed up energy renovation through the digitalization and industrialization of external insulation methods. In concrete terms, after 3D scanning the building, software automates the study phase and panel sizing. The panels are then prefabricated in the workshop using an optimized industrial process. Finally, the panels are delivered to the site and installed without disturbing the occupants or their neighbors.
More generally, I think that our role is not just to innovate or encourage one solution over another. Steel slag, for instance, can only meet 15% of the planet’s needs. So this cannot be the only solution. Our role is to make multi-materials and multi-solutions more widely known, to meet the needs of each structure and each contractor. This is why, in the beginning, within the framework of low-carbon concrete, for instance, we carried out the research internally to really understand the subject in depth, the scope of feasibility in technical, economic, environmental, etc. terms. This understanding of all the solutions allows us to provide the right material in the right place.
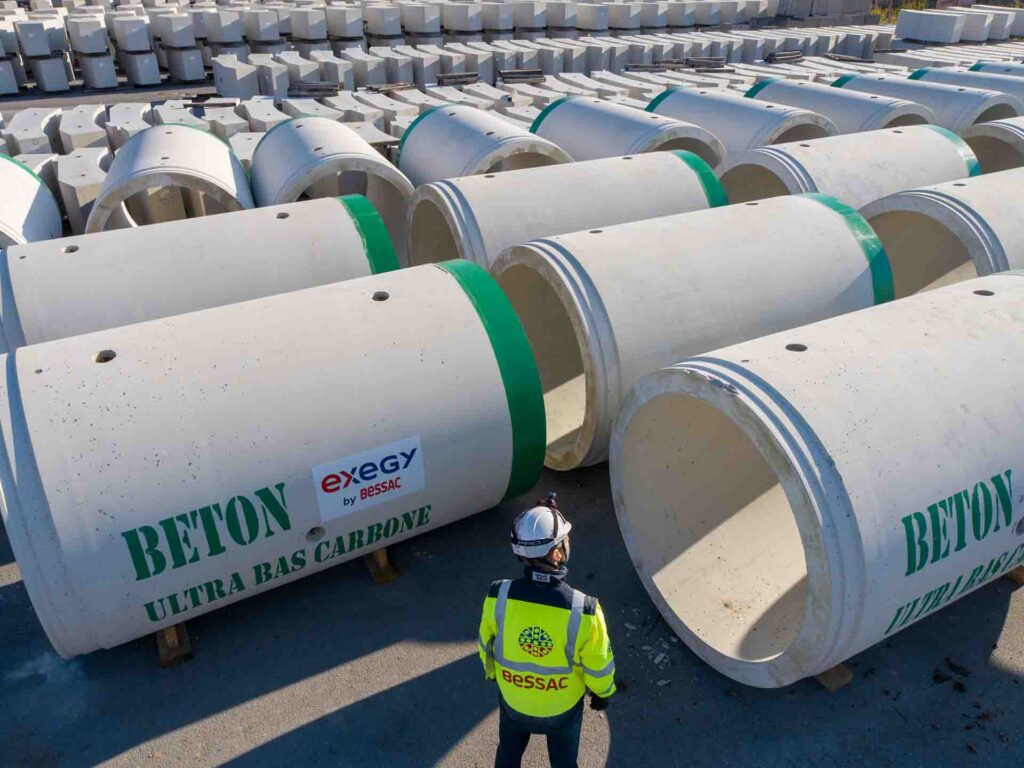
You mentioned renovation, whereas for a long time the Group has been more focused on new construction. Should we stop building to achieve the climate goals and protect biodiversity?
I. S.: You cannot disregard the direct and indirect repercussions of construction on natural habitats. Incidentally, there are ways to limit and compensate for them. This is the aim of zero net land take, a goal set in France by the French Climate and Resilience Act for 2050. At Vinci Immobilier, we have already halved our land take rate since 2020 (from 13% in 2020 to 6% in 2022), abandoning operations that take up the most natural land and making strong progress in the area of urban recycling (28 urban recycling operations started in 2022). In 2022, we launched 29 operations with net deartificialization3, i.e., 40% of our projects. However, nowadays, the theoretical degree of artificialization is set out from the beginning of the project and put into perspective with the other projects in the pipeline.
One of the main levers at our disposal is urban recycling, in other words going to find obsolete real estate, vacant housing units, brownfield sites, etc., and redeveloping them where there is a need. If this is not the case, this real estate will be renatured, thereby compensating for the inevitable artificialization in certain areas. Admittedly, the economic equation is less advantageous here, but it is counterbalanced by a portfolio approach. On average, our projects are becoming more respectful from an environmental point of view, more profitable from an economic point of view, and above all more useful from a social point of view as the main goal remains housing people.
We can clearly see that solutions exist and that sustainable construction has become a key topic for companies and elected officials alike. So why is there still such a disparate level of engagement and action?
I. S.: You’re right, we are still extremely far away from widespread demand. In my view, it’s about a lack of knowledge rather than a lack of willingness on the part of contractors. They don’t always know what they should ask for or what is possible. Sometimes, they censor themselves, presuming that the technology or the budget won’t follow. I want to tell them to make things simpler for themselves. Give us goals rather than thinking about the means. Think performance rather than cement or biomass. If the goals are clear and we think we can achieve them, then our teams and our partners’ teams will innovate together to offer solutions. And not the other way round.
“Our role is to make multi-materials and multi-solutions more widely known, to meet the needs of each structure and each contractor.”
But how can you convince contractors that almost anything is possible?
I. S.: It’s always more comfortable to opt for a solution that has already proven its worth. However, in construction, the projects are essentially made-to-measure. Of course, we have feedback, but nothing is 100% replicable. We must therefore continue to increase the number of projects to show that we can deliver quality. We must take the time to do it and be prepared to invest to obtain convincing proof. Then, I would almost want to say that we must not constantly be looking to innovate but take the time to demonstrate what already exists. This is what we have done with low-carbon concrete in our headquarters. We have taken responsibility for the R&D and implementation, to subsequently be able to convince people of the quality of the approach and roll it out.
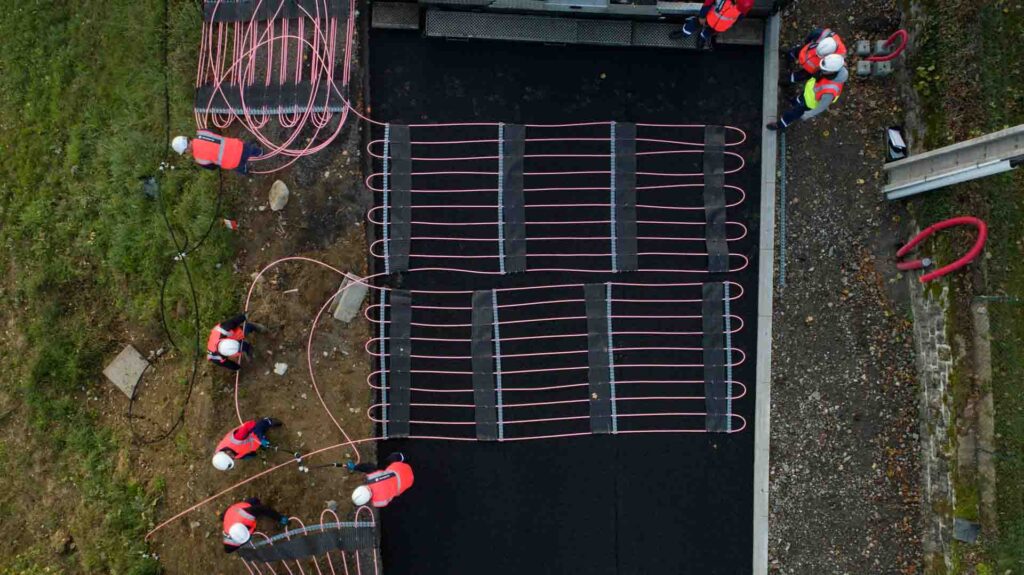
How can regulations contribute to sustainable construction’s development?
I. S.: It cannot be denied that RE2020 and, more generally, all actions — whether restrictive or otherwise — implemented on a state level are driving things forward. I’m thinking in particular of the creation of a Buildings Breakthrough, international cooperation already supported by 18 countries, setting the target of “near zero carbon & resilient buildings” by 2030 for the building sector. In all the countries championing this ambition, we know that governments will support companies working to this end. However, regulations must come at a time when the country is mature enough. Otherwise, it can have quite the opposite effect of discouraging and slowing down innovation. Finally, it is clear that there is still a great deal of disparity from one country to the next in how the regulations are made and enforced. To convince, you have to therefore draw on other — particularly economic — arguments.
“Give us goals rather than thinking about the means.”
A pipe dream (but realistic if we all go for it) for sustainable construction?
I. S.: In my opinion, the biggest obstacle that prevents us from moving forward is indeed economic. People are often looking for project profitability, but this leaves out the fact that the funder of the project is not the same as its builder or occupier. So the whole question is this: for whom is the project profitable? Ideally, it should be profitable for everyone. To achieve this, we must be capable of coming up with funding and organizational models that allow everyone to win, regardless of their position in the value chain. To do so, we will need to overcome organizational barriers and all work toward the same goal: the end purpose of the project. The performance and profitability would then be defined and worked on in relation to this same goal. Incidentally, this is the concept of “sustainable performance” to which we are committed within the Vinci Group.
- Scope 1 encompasses direct emissions on the company’s sites; scope 2 covers indirect emissions, mainly associated with electricity use; and scope 3 relates to upstream and downstream emissions in the value chain.
- Also known as “blast furnace slags,” these are by-products from the iron and steel industry from cast iron manufacture in blast furnaces.
- This transition process consists in restoring the land’s natural functions and therefore requires cleaning it up, making it more permeable, and restoring its nutrients.
Photo credits: © Vinci, © Shortfuse, © Yves Chanoit, © Agence Louise