In August 2023, the President of the United States, Joe Biden, allocated a budget of 1.2 billion dollars (€1.1 billion) in subsidies to two plants that directly capture carbon from the air, one in Louisiana and the other in Texas, run by the oil company Occidental Petroleum. Directly extracted from the atmosphere, the carbon will be processed and buried in rocks deep underground. This strategic shift was explained by Jennifer Granholm, U.S. Secretary of Energy, as follows: “Merely reducing our carbon emissions won’t counteract the escalating impacts of climate change. We must also extract the CO2 we’ve already released into the atmosphere.”
Within this context, we are seeing a real flurry of innovative projects, particularly in the construction sector, which is mobilizing into action, conscious of the significance of the issues at stake and its responsibility. It is therefore the driving force behind numerous projects, characterized by strong cooperation between the different players – research, industries, start-ups, and builders. They are turning to technologies to capture, use, and store the carbon (CCUS, for Carbon Capture, Use and Storage) from industrial emissions directly at the source before it is released into the air. These technologies include carbon capture and storage (CCS) without recovering products from the flue gas treatment and direct air capture (DAC), far from industrial sites. In the latter cases, the CO2 is then “buried” under land or sea, like waste in a landfill. While they are of interest to industrialists, allowing them to reduce their CO2 emissions, these techniques still have to demonstrate that they can be developed at an acceptable cost (see our boxed text).
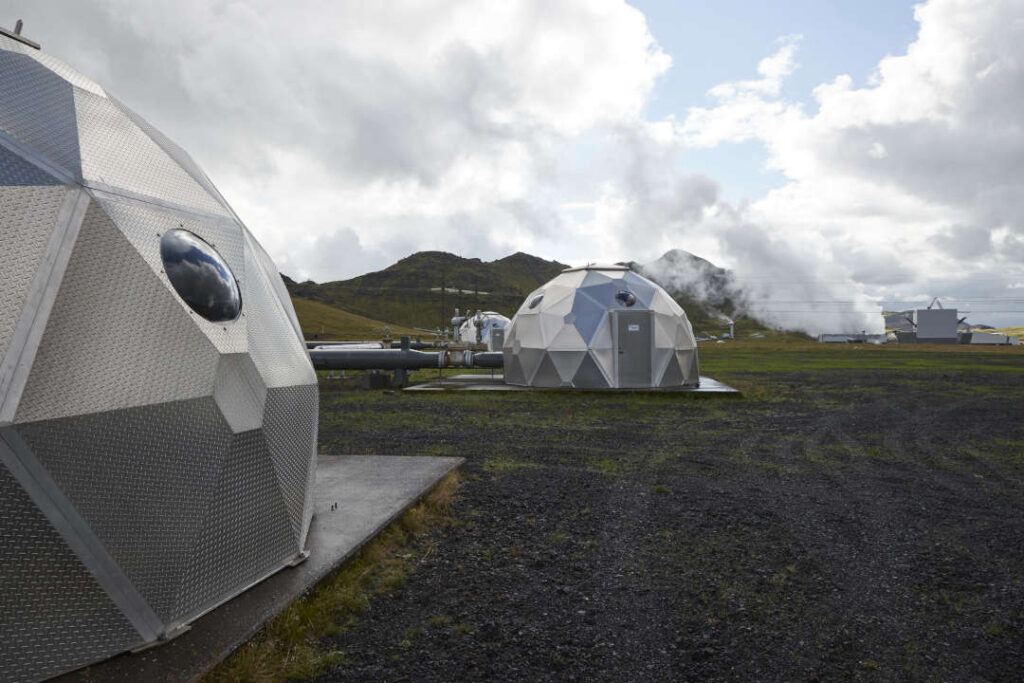
Capturing and storing
CCS technologies aim to recover carbon in order to store it in the long term in gas wells, soils (depending on their nature and thickness: forest, agricultural, degraded, artificialized, etc.), or saline aquifers1 where it is mineralized over time. While this solution makes it possible to store carbon for millions of years, its feasibility nonetheless requires certain conditions to be met. Starting with the availability of capture facilities and transport infrastructure (pipelines) on an extremely large scale, along with less energy-intensive2 technologies whose costs are reduced as the methods become more widespread, bearing in mind that the closer the storage area is to the capture site, the lower the transport costs. The total cost of CO2 capture and storage is estimated to be between €70 and €250 per metric ton depending on the geology of the sites used. By deploying this method in areas where the soil has a high proportion of metallic minerals, the cost per metric ton of CO2 could drop to €120. In sectors composed of non-metallic minerals, its further development would make it possible to increase the number of facilities fivefold and reach €90 per metric ton of CO2.
The Intergovernmental Panel on Climate Change (IPCC) and the International Energy Agency (IEA) estimate that CO2 capture and storage represent pertinent strategies for limiting global warming, even if the target set (capturing 7.6 GtCO2/year by 2050) seems difficult to achieve at present. In France, in an opinion on the governmental CCUS strategy published on November 30, 2023, the High Council on Climate (HCC) estimates that the role of current technologies will necessarily be “limited” insofar as the target of 4 to 8 MtCO2/year does not seem realistic. However, reducing industrial emissions via CCS by 2 to 4 MtCO2/year by 2030 is conceivable. Likewise, reaching 15 to 20 MtCO2/year by 2050 is “consistent with available knowledge.” In this respect, the HCC emphasizes the need to invest as a priority in R&D “to remove uncertainties about France’s geological storage capacities, the technological potential, the impact on water resources, the availability of biomass for BECCS (bioenergy with CCS), and the sizing of the electricity system to take CCS energy needs into account.”
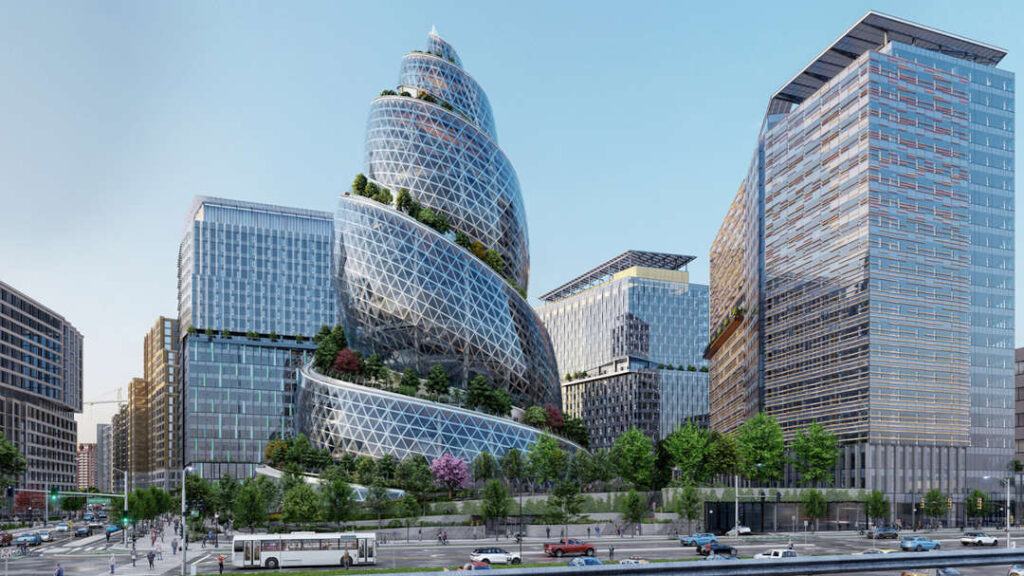
Reusing CO2
Carbon capture and use (CCU) technologies aim to extract CO2 to turn it into a range of products. On its Montalieu-Vercieu site (Isère), Vicat cement works has thus developed a CCU solution, in partnership with Hynamics (EDF subsidiary), with a view to capturing 40% of the CO2 emitted by its cement works’ production, then combining it with the hydrogen produced in a low-carbon way to give decarbonized methanol.
At present, the actors most involved in CO2 capture, use, and storage solutions are cement manufacturers, 70% of whose CO2 emissions come from the rocks used. Carbon capture on site is set to reduce this proportion to 40% by 2050.
Further reading: The impact of embodied carbon across a building’s lifecycle
While capturing carbon without reusing it still has a very high cost and involves a number of risks linked in particular to seismic hazards or CO2 dilution in seawater, reusing it by fixing it in concrete to increase its resistance has, in contrast, the advantage of greatly reducing – by capturing them at source – the emissions from industrial facilities in sectors such as the steel industry, cement manufacturing, energy production, and petrochemicals, which are major CO2 emitters.
For instance, the Canadian company CarbonCure has joined forces with 150 concrete production plants worldwide – including the French firm Lafarge, the Swedish company Thomas Concrete, and the American business Ozinga – to capture carbon and reinject it into a new-generation concrete, which is more resistant and already being used in the construction of warehouses, hospitals, and offices.
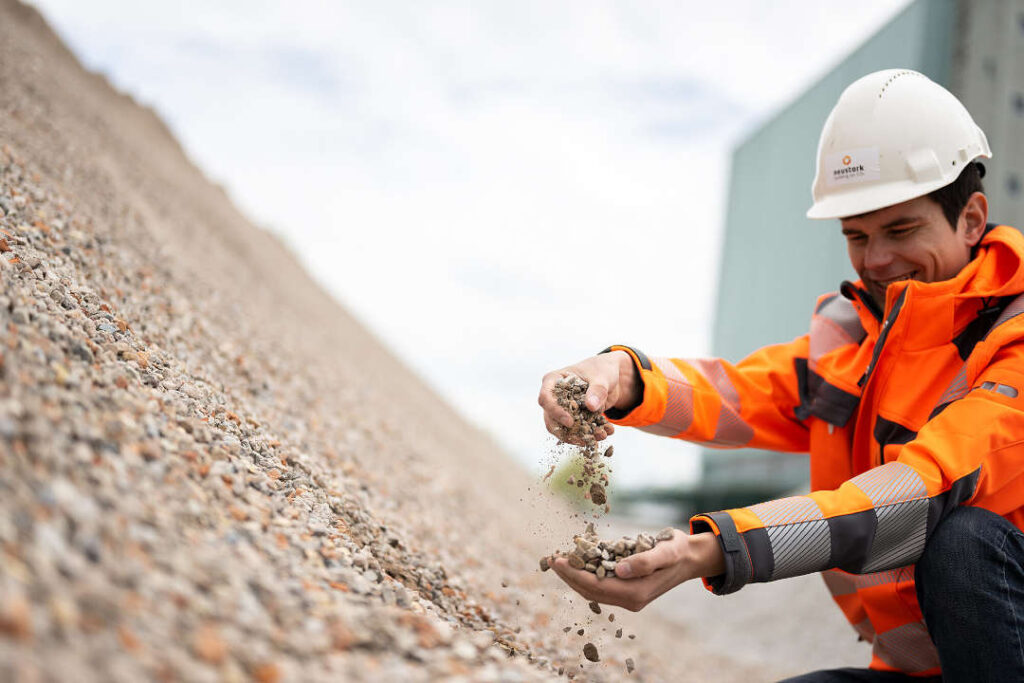
In the same vein, CarbiCrete, another Canadian start-up, has developed carbon-“storing” concrete blocks. Slag from the local steel works is reused as a binder instead of cement by concrete manufacturers. In Switzerland, Neustark has developed a technique for mineralizing carbon in recycled concrete aggregates. In its Zurich laboratories, the company is experimenting with a method to increase CO2 absorption per cubic meter of concrete. As each cubic meter has a carbon cost of 200 kg of CO2, its aim is to manage to capture an equivalent volume (200 kg) in one cubic meter of concrete. This solution is set to be released on the market as of 2025.
Carbon in every form
Concrete is not the one and only carbon recycling solution. It can be converted into calcium carbonate to manufacture sheeting paper, foodstuffs, toothpaste, etc. Viewing carbon as a reusable resource therefore seems the most encouraging approach to date and it is not entirely new… “In fact, industry already incorporates CO2 to manufacture urea, a widely used fertilizer that can also serve as a precursor for many plastics and salicylic acid, which is used in the composition of aspirin and certain acne products, along with polycarbonates, polymers found in CDs, DVDs, and glasses lenses. It’s a matter of taking these uses even further and inventing new ones,” explains Marc Robert, a researcher at the Laboratory of Molecular Electrochemistry3.
Among these innovations, microalgae represent a promising alternative not only for capturing CO2 by photosynthesis (1 m3 of microalgae, like phytoplankton in the sea, is said to possess the same photosynthesis capacity as 80 to 100 trees), but also producing energy (biomass), oxygen, sugar, proteins and trace elements, and therefore food supplements. Microalgal residue could have another application by creating bio-bitumen for Public Works.
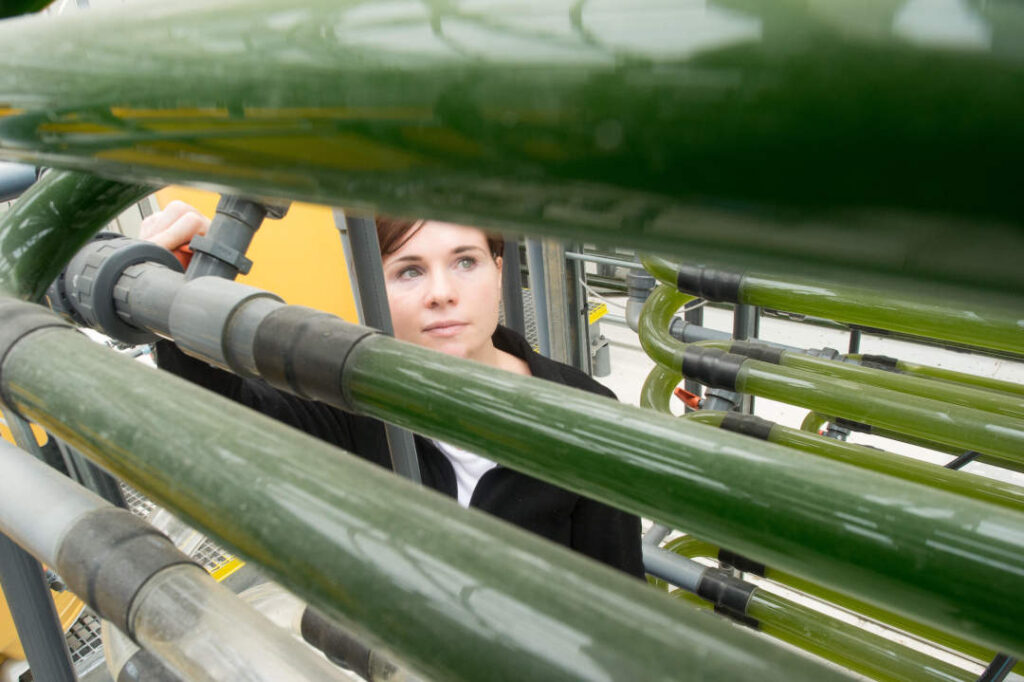
CO2 capture and reuse hold promising prospects. Nonetheless, the investment and operating costs remain extremely high and, from an environmental point of view, most of the capture technologies employed continue to consume large amounts of materials and energy. Moving to a wider scale will require removing these obstacles.
1. Geological formation made up of porous sedimentary rocks containing salt water. 2. Converting 25% of CO2 currently consumes as much hydrogen as powering a cement kiln. 3. https://lejournal.cnrs.fr/articles/le-co2-une-ressource-a-exploiter#footnote1_yfdnhie
How is CO2 captured from the atmosphere?There are two key forms of CO2 capture, one (CCS) from industrial emissions (70% of CCUS) and the other in which carbon dioxide is extracted from the atmosphere, far from industrial sites (DAC, direct air capture).
The capture and industrial separation of CO2 is not a new technology. It has existed for over 50 years in oil operations, and more recently in the cement and steel industries. Silica fumes, for instance, produced during silicon and ferrosilicon manufacturing, was discharged into the atmosphere until the 1980s. Since then, it has been reused as a component in concrete.
Three capture methods are used in industry:
- Precombustion capture consists in decarbonizing the fuel before its combustion. The treatment leads to the production of water, carbon, and hydrogen, but it is considered to be too expensive.
- With post-combustion flue gas capture, the flue gas is “washed” to extract the CO2 from the emissions arising from the fuel (natural gas, oil, coal, etc.). Innovations in this field are looking to minimize energy consumption and reduce the size of the facilities and investment.
- Oxy-fuel combustion capture uses pure oxygen in the combustion, which makes it possible to obtain flue gas more concentrated in CO2 (around 90%). The CO2 is therefore easier to separate from the steam with which it is mixed.
DAC-Direct Air Capture directly captures the CO2 in the atmosphere but far from industrial emissions. It is therefore much more diluted and thus more expensive to extract. There are 15 direct air capture facilities in operation worldwide, with a production of over 9,000 tCO2/year.
Photo credits: © Orjan Ellingvag / Alamy, © Arnaldur Halldorsson/Bloomberg / GettyImages, © Amazon/NBBJ © Neustark, © imageBROKER/Guenter Fischer / Alamy